ScanWorks Processor-Controlled Test
CPU - the most powerful instrument
Put the most powerful instrument on your board – the CPU – to work performing structural and functional diagnostics, debug routines and tests all in one pass.
Embedded in that CPU on your circuit board are the instruments that are critical for overcoming today’s design challenges. Given the complexity of board designs and chips, you need access to this on-chip technology to diagnose, debug and test your designs. One of the tools that makes up the ScanWorks platform for embedded instruments is Processor-Controlled Test (PCT). It takes advantage of the CPU’s debug port for access to the circuit board so it can perform board debug, device initialization, at-speed functional test with structural diagnostics and much more. PCT is just one of several ScanWorks tools which address every stage in a product’s life cycle.
The flexible BST licensing model ensures cost-efficient, agile and strategic deployment of tools throughout your enterprise; in board design prototyping, manufacturing test, and field return repair environments. Deploy just the tools you need in each domain. No surpluses. No slack. Optimum savings.
But what really opens up your future destinations is that ScanWorks BST runs on the ScanWorks Platform, host to a range of other complementary ScanWorks test technologies that can extend board quality control way beyond the capabilities of any boundary scan tester.
A single platform for board validation, test and debug.
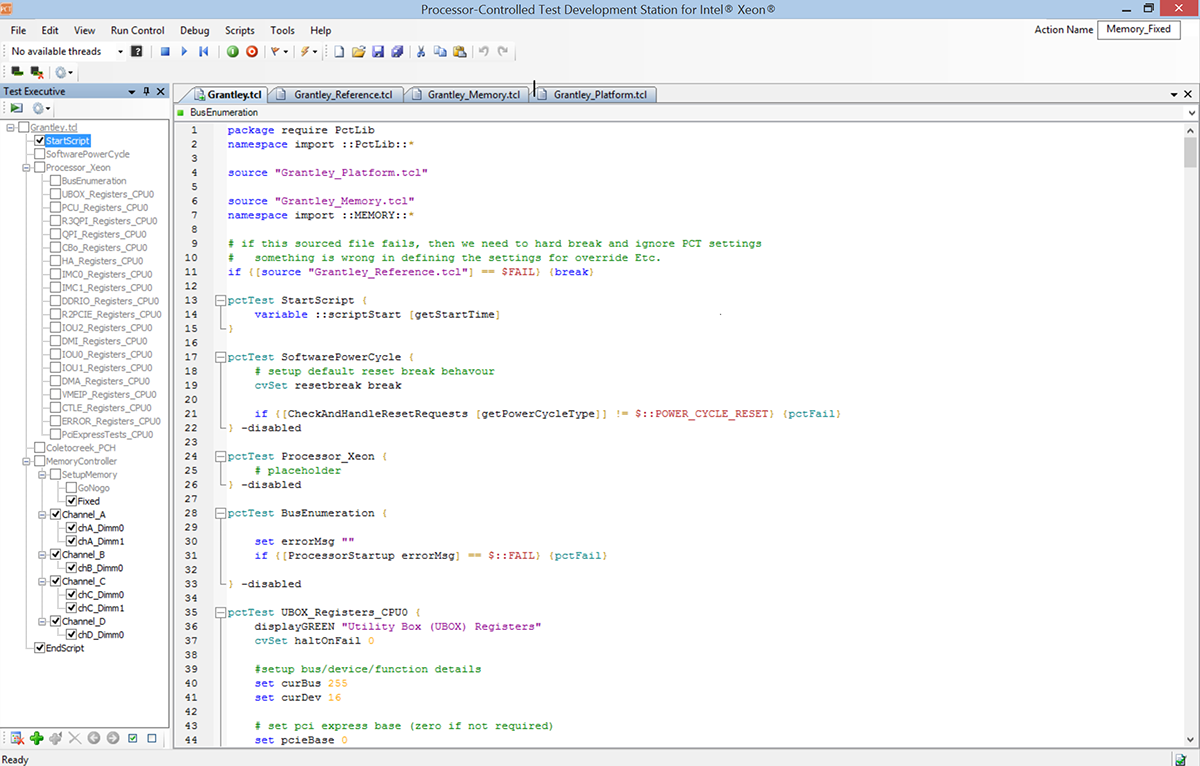
Processor-Controlled Test Development Software
With the PCT Development software, design or test engineers can debug prototypes using low-level control of the processor, as well as develop test and diagnostics tools for manufacturing and repair facilities. Testing platforms designed with Intel® Architectures (IA) can be extremely difficult and testing memories near impossible, however PCT targets Intel Core® and Intel Xeon® to provide better (no BIOS), faster (automated), and precise (bit level) functional tests.
- Control the processor directly through the JTAG port or the processor’s debug port, running code at full speed
Memory testing for Intel-based Core and Xeon designs is automated, using unique methods within PCT tool
Memory diagnostics to rank, device and bit-level
For Intel customers, BIOS independence is a key value, and no BIOS is needed to use PCT in any product life-cycle phase
I/O tests for Intel-based Core and Xeon design are automated with PCT automation test generation
User Control – Create additional bus tests, other memory tests and I/O scripts, using standard TCL scripting language
- Save tests for specific components in a library for re-use on other boards that use those components
Processor-Controlled Test Manufacturing Software
With the PCT Manufacturing software, test operators with minimal training can apply structural and functional tests to circuit boards on the assembly line. The return on investment is very fast due to the lower costs for hardware, software and labor. Re-use of tests developed during prototype stages also keeps engineering costs down.
- Apply any test that is exported from a PCT development environment, along with some diagnostic guidance
- Increase structural test coverage by running functional test code at full processor speed
- Program flash devices using the speed of the processor
- Test production boards without the need for complex and expensive fixtures
- Re-use test and programming actions that were already developed during a product’s design stage
- Easily train new operators on the simple graphical user interface
- Optionally run tests from a test executive, using an API
Processor-Controlled Test Embedded Diagnostics
With embedded PCT, information about difficult-to-reproduce failures in the field can be captured for analysis.
- Embed functional-test IP in the board to store information for use in diagnosing failures that occur in the field
- Access diagnostics remotely, using a PC interface of test executive
Related Products
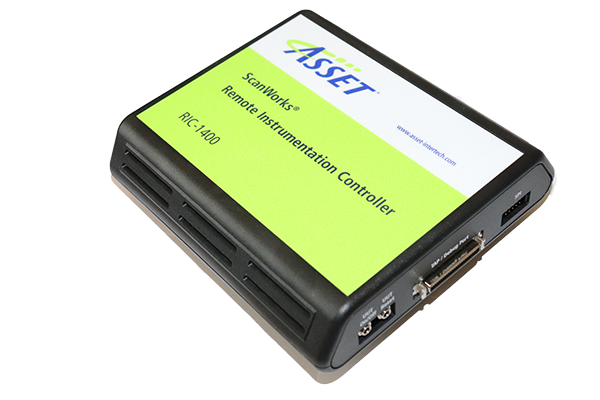
The ScanWorks platform for embedded instruments is supported by a wide variety of hardware controllers and accessories with which engineers can connect ScanWorks to their unit under test (UUT). Hardware is available for development, production and repair environments. The test platform required for ScanWorks is either a standard PC or a system with a built-in (embedded) JTAG controller.
Related eResources
In the paper, faults are inserted on an Intel® Shark Bay platform, and the ScanWorks® Processor-Controlled Test product is used to detect a myriad of faults. Real life examples always provide for more clarity as shown in this paper.